Ball grid array, also known as BGA, packaging is a type of surface mount packaging for electronic components.
What is it?
The name pretty well describes exactly what BGA packaging consists of.
It is basically a grid of balls made of solder on the underside of an integrated circuit that are then soldered to pads on a circuit board.
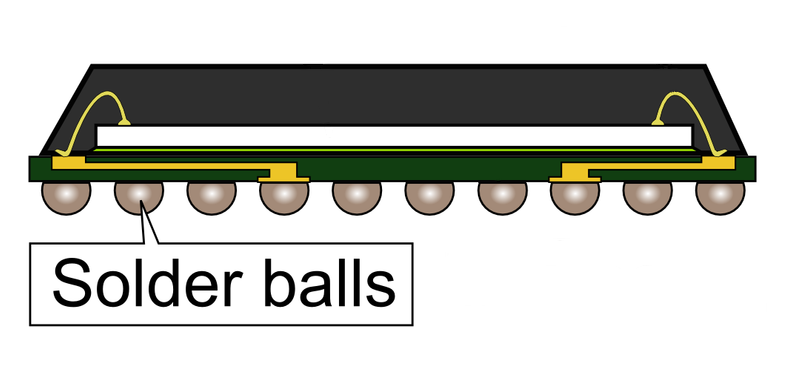
More Connections
One of the advantages of the BGA package is that the whole bottom of the integrated circuit can be used for external connections.
In contrast, many other types of integrate circuit packages only use the perimeter of the package for these external connections.
There are several other advantages for the ball grid array (BGA) package style.
Better Thermal Conduction
Another advantage of BGA packages is better heat conduction vs other types of packages with the standard “leg” type of connections.
With the BGA package, heat is better transferred to the circuit board, this helps keep BGA packaged integrated circuits cooler.
Because of this heat transfer advantage, you will often see BGA packaging in integrated circuits that consume quite a bit of power.
Some examples of these high power integrated circuits are CPUs (central processing units) and GPUs (graphics processing units).
CPUs and GPUs also normally have a lot of pins, so they can take advantage of the extra external connection capacity of the BGA package as well.
Lower Inductance Connections
The last advantage we are going to discuss is the lower inductance of the package leads.
Too much inductance is a problem for electronic circuits, especially high speed circuits.
If there is too much inductance important electronic signals will become distorted at high speeds.
Lower inductance reduces these effects and allows designing integrated circuits that can run at higher speeds.
Disadvantages
Along with these advantages of BGA packaging, there are some disadvantages that should be taken into account.
Thermal Stress
One of the main disadvantages of the BGA package is that the electronic connections are not very flexible.
This might seem like a good thing, but it does present issues that can affect the reliable operation of the circuit.
The different rates of thermal expansion of the BGA and the printed circuit board can cause mechanical stress between the two.
This can cause cracks in the solder joints between the BGA and the printed circuit board.
This can be reduced in many cases by using a plastic integration circuit package material instead of something like ceramics.
The plastic package will generally have a thermal expansion rate that is closer to the printed circuit board.
Vibration and External Stress
Vibration can also cause the same stresses and potential cracking, so BGAs may not be a good package choice in environment where there is a lot of vibration.
Hard to Inspect
Another disadvantage of BGA packaging is that it is hard to view the solder connections since they are on the underside of the integrated circuit.
Because of this it is hard to identify issues with the quality of the soldered connections.
This can cause an issue when inspecting newly soldered components for quality assurance purposes or when trying to diagnose some failure in an existing electronic device.
There are some devices that can be used to help inspect the BGA solder connections, such as x-ray machines, CT scanning machines, and special microscopes.
These are generally much more expensive than the equipment required to inspect other, more traditional, solder connections.
Repair of Bad Connections
If there are issues with the solder connections on a BGA package integrated circuit there are tools, called BGA rework stations, that are designed to assist in repairing soldering issues on BGA packages.
Expensive Equipment
The last disadvantage we are going to touch on is that the equipment needed to solder BGA packages reliably is specialized and expensive.
If the package is small hand soldering methods can be used for low volume production or repair work, but in most cases it is not feasible.
More recently, there have been some do it yourself techniques that have been developed to allow soldering BGAs reliably without expensive equipment.
There methods use more traditional surface mount tools like heat guns as well as other, less traditional, heat sources like toaster ovens and electric skillets.
Conclusion
BGA packages can be a good fit depending of the requirements of the electronic circuit being designed.